Common pipe insulation materials include fiberglass, mineral wool, rubber, and foam options, each serving specific temperature and moisture requirements. Fiberglass offers excellent thermal resistance and non-combustibility, while mineral wool excels in fire protection and mold prevention. Rubber insulation provides flexibility and moisture resistance, making it suitable for both indoor and outdoor applications.
Protective coverings range from rigid metal shields to flexible wraps, with proper installation requiring specific tools and safety equipment. Regular maintenance, including biannual inspections and periodic replacement every 10-15 years, guarantees ideal performance.
Understanding the complete scope of installation methods and industry standards reveals critical factors for system longevity.
Highlights
- Common pipe insulation materials include fiberglass, mineral wool, rubber, and foam, each offering specific benefits for different plumbing applications.
- Rigid metal covers provide superior mechanical protection and thermal efficiency for insulated piping systems exposed to physical damage.
- Weather-resistant coatings like polyurethane, epoxy, and silicone protect plumbing systems from environmental damage and extend operational lifespan.
- Proper insulation can reduce heat loss by up to 80% in hot water systems while minimizing energy costs.
- Regular maintenance and inspections every 6-12 months ensure insulation effectiveness and compliance with safety regulations.
Understanding Basic Pipe Insulation Materials
Selecting the right pipe insulation material is essential for ensuring ideal system performance and energy efficiency. Modern plumbing systems offer several types of pipe insulation, each designed to protect your pipes under specific conditions and requirements.
Common Types of Pipe Insulation:
- Fiberglass pipe insulation provides excellent thermal resistance through its non-combustible composition, making it suitable for various temperature ranges and applications.
- Mineral wool insulation, derived from natural or synthetic minerals, delivers superior fire resistance and mold prevention, particularly in high-temperature environments.
- Rubber pipe insulation features flexibility and moisture resistance, allowing for effective protection in both indoor and outdoor installations.
- Foam pipe insulation utilizes a cellular structure that creates an efficient thermal barrier while remaining cost-effective and simple to install.
Selection Considerations:
- Temperature requirements
- Moisture exposure levels
- Installation environment
- Cost constraints
- Fire safety requirements
Each insulation type offers distinct advantages: fiberglass excels in general applications, mineral wool performs well in high-heat scenarios, rubber provides superior moisture protection, and foam delivers cost-effective solutions for residential systems.
Understanding these characteristics enables proper material selection based on specific application needs.
Common Types of Protective Coverings
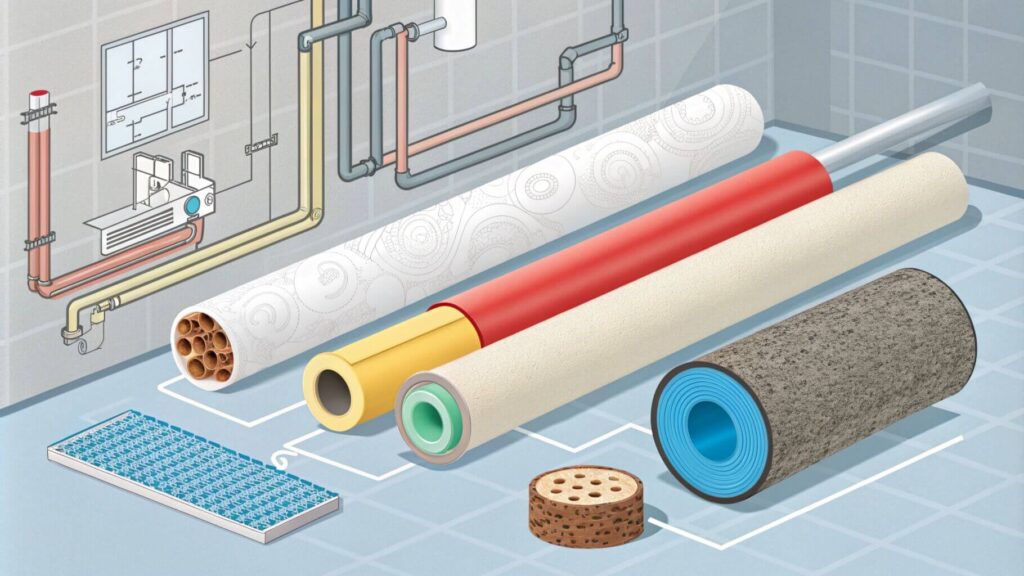
Protective coverings for pipes come in three primary configurations: rigid metal covers, flexible wraps, and weather-resistant coatings, each serving specific installation needs and environmental conditions.
Rigid metal covers, typically made from aluminum or stainless steel, provide superior mechanical protection while maintaining thermal efficiency through their integrated insulation properties.
Flexible wrap solutions and weather-resistant coatings offer adaptable protection options, with wraps conforming to irregular pipe shapes and coatings creating waterproof barriers against environmental factors.
Rigid Metal Pipe Covers
Among the most reliable protective solutions for insulated piping systems, rigid metal pipe covers stand as a cornerstone of industrial and commercial applications. These durable covers, typically manufactured from galvanized steel or aluminum, provide essential protection against physical damage while ensuring system longevity in demanding environments.
The implementation of rigid metal pipe covers serves multiple critical functions in mechanical rooms and industrial settings. First, they create a robust barrier that helps maintain consistent temperatures within insulated piping systems, particularly those carrying steam or hot water. Additionally, these covers contribute notably to fire protection by containing heat and minimizing the potential for fire spread along pipe runs.
Installation options include:
- Pre-formed sections for standard pipe sizes
- Custom-fabricated options for unique configurations
- Specialized fittings for corners and joints
Key Benefits:
- Enhanced physical protection against impacts and wear
- Improved noise reduction in operational environments
- Superior weather resistance for exterior applications
- Professional aesthetic appearance
- Extended insulation life through moisture prevention
When properly installed, these covers provide an all-encompassing solution that combines practical protection with regulatory compliance, making them ideal for both new installations and system upgrades.
Flexible Wrap Solutions
While rigid metal covers provide robust protection, flexible wrap solutions offer a versatile alternative for pipe insulation and protection needs. These adaptable materials, including Nitrile Foam Rubber Insulation and Polyethylene Foam Pipe Insulation, accommodate various pipe sizes and configurations with ease.
Among the most effective options, Armaflex insulation, made from nitrile foam, delivers superior moisture resistance and thermal protection for temperatures up to 105°C. The material’s self-sealing properties guarantee consistent coverage and simplified installation.
Polyethylene foam wraps, known for their cost-effectiveness, present an accessible solution for residential applications where insulation thickness can be customized based on specific requirements.
For outdoor installations exposed to UV exposure, EPDM foam rubber insulation provides enhanced durability with built-in ultraviolet protection. This specialized material maintains its protective properties in high-temperature environments up to 150°C.
Additionally, mineral wool wraps serve as an alternative flexible solution, particularly in industrial settings where fire resistance is paramount. These materials can be easily adjusted to different pipe sizes while maintaining ideal thermal performance and safety standards throughout various plumbing applications.
Weather-Resistant Coating Options
Weather-resistant coatings represent an essential layer of defense for insulated pipe systems, with polyurethane, epoxy, and silicone-based solutions leading the market in protective capabilities.
- These specialized coatings create barriers that shield plumbing systems from environmental damage, extending their operational lifespan and maintaining system integrity.
- Polyurethane coatings excel in outdoor applications due to their superior resistance to UV radiation and remarkable flexibility, which allows them to adapt to pipe movement without cracking.
- Epoxy solutions provide exceptional chemical-resistant properties and can withstand significant temperature fluctuations, making them ideal for both industrial and residential applications where exposure to harsh conditions is common.
- Silicone-based formulations offer superior waterproofing capabilities and exceptional adhesion properties, particularly in environments with extreme temperature variations.
These coatings form a moisture-resistant seal that prevents water intrusion and subsequent corrosion of underlying pipe materials.
Maintenance Requirements:
- Regular inspection of coating integrity
- Periodic reapplication based on manufacturer specifications
- Immediate repair of any damaged sections
- Professional assessment of coating performance every 2-3 years
- Documentation of maintenance procedures and schedules
Thermal Performance and Heat Loss
Pipe insulation’s thermal performance plays a fundamental role in maintaining system efficiency and reducing energy costs. The effectiveness of insulating pipes depends primarily on thermal conductivity, which measures how easily heat transfers through a material, and the R-value, indicates resistance to heat flow. Higher R-values signify better insulation performance, resulting in reduced heat loss through water pipes.
Proper insulation can deliver significant benefits for plumbing systems:
- Reduces heat loss by up to 80% in hot water systems, maintaining desired water temperatures throughout the distribution network.
- Minimizes energy consumption and operating costs by preventing unnecessary heat transfer through pipe walls.
- Protects pipes from temperature fluctuations and potential freezing in cold climates.
Regular inspection of insulation materials is essential for maintaining ideal thermal performance. Damaged or deteriorating insulation can compromise the system’s efficiency and lead to increased energy consumption.
The thickness of insulation directly correlates with its effectiveness; thicker insulation typically provides better thermal resistance. When selecting insulation materials, such as fiberglass or mineral wool, consideration should be given to both their thermal conductivity ratings and environmental conditions.
Installation Methods and Best Practices
Installing pipe insulation requires proper sealing techniques, including the careful application of adhesive or vapor barrier tape at all joints and seams.
Professional-grade tools, such as utility knives, measuring tapes, and spreaders, guarantee precise cuts and secure attachments during the installation process.
Personal protective equipment (PPE), including safety glasses, gloves, and dust masks, must be worn when handling insulation materials to prevent skin irritation and respiratory issues.
Proper Sealing Techniques
Effective sealing techniques form the cornerstone of proper pipe insulation installation, directly impacting both system efficiency and longevity. When addressing insulation needs, professionals must guarantee tight-fitting sections that eliminate gaps where heat loss and moisture can occur.
Self-sealing options, such as nitrile foam rubber, provide an efficient solution by creating an immediate, secure seal without additional adhesives.
For ideal insulation performance, follow these critical steps:
- Install sections with precision, ensuring tight butt joints and proper compression at all connecting points.
- Secure materials using appropriate taping methods or mechanical fasteners, particularly in areas subject to movement.
- Apply protective covering or UV-resistant materials for outdoor installations to prevent degradation.
Regular maintenance and inspection remain essential components of proper sealing techniques. Technicians should examine sealed areas periodically for signs of wear, moisture infiltration, or separation between sections.
When issues are detected, immediate remediation prevents further deterioration and maintains system efficiency. For outdoor applications, additional attention must be given to weather-resistant barriers and proper drainage to guarantee long-term performance and protection against environmental factors.
Tools and Safety Equipment
Successful pipe insulation projects depend heavily on having the right tools and safety equipment readily available before beginning any installation work.
Essential tools include utility knives for precise cutting, measuring tapes for accurate sizing, and appropriate adhesive or tape for securing insulation materials to pipes.
Required Safety Equipment:
- Protective gloves to shield hands from sharp edges
- Safety goggles to protect eyes from debris
- Respiratory protection when working with fibrous materials
- Appropriate work clothing to cover exposed skin
Installation Tools:
- Heat gun for working with rubber or foam insulation
- Scissors or shears for clean cuts
- Metal measuring tape
- Marking pencils or markers
- Adhesive applicators
Working Environment Requirements:
- Proper lighting in work areas
- Stable ladders or scaffolding for elevated installations
- Adequate ventilation when using adhesives
- Clean, dry workspace around pipes
Before beginning installation, verify all tools are in good working condition and that safety equipment fits properly.
Organize tools within easy reach to maintain efficiency during the installation process, and always keep first aid supplies nearby in case of minor injuries.
Maintenance and Replacement Guidelines
Proper maintenance of pipe insulation systems demands regular inspection and timely replacement to guarantee peak performance and protection.
Regular assessments help identify wear, damage, or moisture intrusion that could compromise insulation effectiveness, particularly in outdoor installations where environmental factors play an essential role.
To secure ideal performance and longevity of pipe insulation systems, follow these essential guidelines:
- Conduct thorough inspections every 6-12 months, paying special attention to outdoor pipes with UV-protective coating, and document any signs of deterioration or damage.
- Replace insulation materials every 10-15 years, or earlier if visible signs of wear such as fraying, cracking, or mold growth are present.
- Maintain detailed maintenance records, including dates of inspection, replacement activities, and observed conditions.
When replacing insulation, select appropriate materials with a minimum thickness of 19mm for outdoor applications.
Consider environmental factors such as temperature fluctuations, humidity levels, and UV exposure when choosing replacement materials.
Implementation of a systematic maintenance schedule helps prevent costly repairs from frozen pipes or leaks while maintaining consistent insulation performance throughout the system’s lifespan.
Environmental Impact of Insulation Choices
The environmental consciousness of insulation material selection plays a pivotal role in sustainable plumbing systems. Modern insulation manufacturing processes have evolved to incorporate significant amounts of recycled content, particularly in materials like fiberglass, which can contain up to 60% recycled glass components.
Key Environmental Considerations:
- Eco-friendly insulation options, such as mineral wool, require minimal energy during installation and manufacturing processes, reducing overall environmental impact.
- High-performance materials like phenolic foam contribute to decreased greenhouse gas emissions throughout their operational lifespan.
- Sustainable insulation solutions incorporating recycled content deliver dual benefits: waste reduction and improved energy efficiency.
Impact on Building Performance:
- Enhanced thermal protection leads to reduced heating and cooling requirements.
- Lower energy consumption results in decreased carbon footprint over time.
- Compliance with green building standards improves overall system sustainability.
When selecting insulation materials, contractors should prioritize options that balance performance with environmental responsibility.
The integration of recycled materials and energy-efficient manufacturing processes guarantees that modern plumbing systems contribute positively to environmental conservation while maintaining peak functionality and protection.
Cost Comparisons Among Material Options
While environmental considerations shape material selection, budget constraints often guide final purchasing decisions. Cost comparisons among different insulation types reveal significant variations in pricing, with each material offering distinct advantages for specific industrial applications.
When evaluating common pipe insulation materials, three key price points emerge:
- Rubber insulation (Armaflex): Most economical at £2.70-£2.97, making it ideal for both residential and commercial projects requiring moisture resistance.
- Phenolic Foam (Kingspan Kooltherm): Mid-range option at £4.44, delivering superior thermal performance and moisture protection.
- Fiberglass solutions (Isover Climpipe): Premium choice at £5.23, offering balanced performance and durability.
Foam insulation stands out in the DIY market segment, with six-foot lengths typically priced under £10, making it accessible for homeowners and small contractors.
Mineral wool options like Rockwool occupy the middle tier at £4.79-£5.27, providing excellent fire resistance for commercial applications.
These price variations reflect differences in material composition, manufacturing processes, and performance characteristics, allowing contractors to select appropriate solutions based on project requirements and budget constraints.
Safety Regulations and Industry Standards
Safety regulations and industry standards consistently form the backbone of pipe insulation practices across commercial and industrial applications. These guidelines, established by organizations like NAIMA, guarantee that insulation materials meet specific performance requirements and safety criteria for protecting plumbing systems.
Key Compliance Requirements:
- R-value specifications: Insulation must achieve minimum thermal resistance ratings based on pipe size and operating temperature.
- Material composition: Non-combustible materials are mandatory for specific applications, particularly in fire-sensitive areas.
- Installation techniques: Proper fitting, sealing, and securing methods must follow prescribed industry protocols.
Quality Control Measures:
- Regular inspections to verify compliance with safety regulations.
- Documentation of material certifications and installation procedures.
- Verification of recycled content percentages in materials like fiberglass and mineral wool.
Professional installation teams must maintain strict adherence to these standards through:
- Proper material selection based on application requirements.
- Correct thickness and density calculations.
- Implementation of appropriate vapor barriers.
- Documentation of installation procedures.
- Periodic maintenance checks to guarantee continued compliance with regulations.
Following these standards not only guarantees legal compliance but also maximizes system efficiency and longevity.
Frequently Asked Questions
What Are the Different Types of Pipe Insulation?
Common pipe insulation types include foam insulation, fiberglass batts, reflective insulation, rubber sleeves, mineral wool, and air gap systems. Each offers unique thermal protection properties and installation characteristics for various applications.
What Kind of Insulation Is Used in Plumbing?
Plumbing systems commonly utilize foam, rubber, and fiberglass insulation, selected based on thermal conductivity ratings and moisture barrier properties. These materials offer energy efficiency benefits while providing cost-effective pipe protection during installation.
What Type of Insulation Is Used in Pipelines?
Common pipeline insulation materials include fiberglass, rubber, mineral wool, phenolic, and polyethylene foam, offering thermal efficiency and moisture barriers. These solutions provide energy savings while maintaining ideal installation techniques and soundproofing properties.
What Is the Best Insulator for Water Pipes?
Polyethylene foam stands out as the best water pipe insulator, offering superior energy efficiency, cost-effectiveness, and material durability. Its low thermal conductivity, easy installation, and minimal environmental impact make it the ideal choice.
Final Thoughts
Proper pipe insulation and protection remain essential elements in maintaining efficient, durable plumbing systems across residential and commercial applications. The selection of appropriate materials, combined with proper installation techniques and regular maintenance, guarantees ideal thermal performance and system longevity.
Industry standards and environmental considerations continue to shape best practices, while cost-effectiveness and energy efficiency drive innovation in insulation technologies. These factors collectively determine the success and sustainability of modern plumbing infrastructure.